Management Lean Manufacturing : optimisez vos processus de production
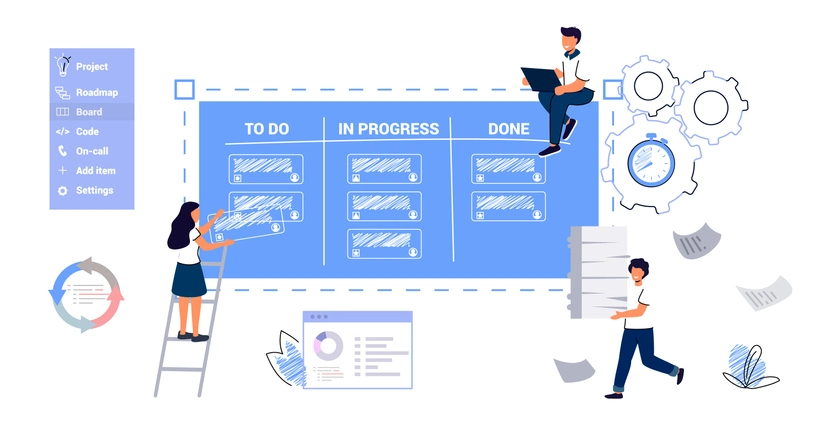
Dans un monde économique de plus en plus compétitif, les entreprises manufacturières doivent constamment chercher des moyens d’améliorer leur efficacité opérationnelle. Le management Lean Manufacturing s’est imposé comme une approche incontournable pour optimiser les processus de production, réduire les coûts et augmenter la valeur pour le client. Cet article vous présente les principes fondamentaux du Lean, ses avantages concrets et une méthodologie pas à pas pour l’implémenter dans votre organisation.
Sommaire
- Qu’est-ce que le management lean manufacturing ?
- Les principes fondamentaux du lean manufacturing
- Différences entre lean manufacturing et méthodes traditionnelles
- Les avantages du lean manufacturing pour les entreprises
- Comment mettre en place le lean manufacturing dans votre organisation ?
- Conclusion
Qu’est-ce que le management lean manufacturing ?
Définition et origine du lean manufacturing
Le Lean Manufacturing est une approche systématique visant à éliminer les gaspillages tout en créant de la valeur pour le client final. Cette méthodologie trouve ses racines dans le Toyota Production System (TPS), développé au Japon après la Seconde Guerre mondiale par Taiichi Ohno et Eiji Toyoda. Face à des ressources limitées, Toyota a développé une philosophie centrée sur l’élimination des activités sans valeur ajoutée et l’optimisation des processus.
Le terme “Lean” (maigre en anglais) a été popularisé dans les années 1990 par le livre “The Machine That Changed the World” de James Womack et Daniel Jones, qui documentait comment cette approche permettait à Toyota de produire des véhicules de meilleure qualité avec moins de ressources que ses concurrents occidentaux.
Les principes fondamentaux du lean manufacturing
Le Lean Manufacturing repose sur cinq principes clés :
- Définir la valeur du point de vue du client : comprendre ce que le client est prêt à payer et ce qui constitue une valeur ajoutée réelle.
- Identifier la chaîne de valeur : cartographier l’ensemble des étapes nécessaires pour transformer les matières premières en produits finis, en identifiant les activités à valeur ajoutée et sans valeur ajoutée.
- Créer un flux de production continu : organiser les processus pour que les produits circulent sans interruption ni attente.
- Mettre en place un système tiré (pull) : produire uniquement ce qui est demandé par le client, quand il le demande.
- Rechercher la perfection : s’engager dans une démarche d’amélioration continue (Kaizen) pour constamment optimiser les processus.
Différences entre lean manufacturing et méthodes traditionnelles
Aspect | Management traditionnel | Lean Manufacturing |
---|---|---|
Production | Par lots importants | Flux continu, petites séries |
Stocks | Élevés (sécurité) | Minimaux (Juste-à-temps) |
Qualité | Contrôle en fin de processus | Intégrée à chaque étape (Poka-Yoke) |
Amélioration | Projets ponctuels | Amélioration continue quotidienne |
Organisation | Hiérarchique | Équipes autonomes |
Gaspillages | Tolérés | Systématiquement éliminés |
Contrairement aux approches traditionnelles qui privilégient l’utilisation maximale des équipements et la production en grandes séries, le Lean Manufacturing se concentre sur la fluidité des opérations et l’élimination des gaspillages pour mieux répondre aux besoins réels des clients.
Les avantages du lean manufacturing pour les entreprises
Réduction des gaspillages et des coûts
Le Lean Manufacturing identifie huit types de gaspillages (ou “muda” en japonais) qui doivent être éliminés :
- Surproduction : produire plus que nécessaire ou avant que ce soit nécessaire
- Temps d’attente : périodes d’inactivité des personnes, machines ou produits
- Transports inutiles : déplacements évitables de matières ou produits
- Traitements inutiles : étapes qui n’ajoutent pas de valeur pour le client
- Stocks excessifs : matières premières, encours ou produits finis en excès
- Mouvements inutiles : déplacements évitables des opérateurs
- Défauts et retouches : erreurs nécessitant une correction
- Sous-utilisation des talents : gaspillage des idées et compétences des employés
En s’attaquant méthodiquement à ces gaspillages, les entreprises réduisent significativement leurs coûts opérationnels. Par exemple, la mise en place du Juste-à-temps (JIT) permet de diminuer les coûts de stockage, tandis que l’amélioration de la qualité réduit les coûts liés aux défauts et aux retouches.
Amélioration de la qualité et de la productivité
Le Lean Manufacturing intègre la qualité directement dans le processus de production plutôt que de la contrôler a posteriori. Cette approche, qui s’appuie sur des outils comme le Poka-Yoke (détrompeurs) ou l’Andon (système d’alerte visuelle), permet de détecter et corriger les problèmes à la source.
La productivité s’améliore également grâce à l’élimination des d’attente et des goulots d’étranglement, ainsi qu’à la standardisation des meilleures pratiques. De plus, la maintenance préventive des équipements (TPM - Total Productive Maintenance) et le suivi des performances via l’OEE (Overall Equipment Effectiveness) permettent l’amélioration de cette productivité.
Des entreprises ayant adopté le Lean rapportent régulièrement des gains de productivité de 15 à 30% dans les premiers mois d’implémentation.
Augmentation de la satisfaction client
En se concentrant sur la valeur perçue par le client, le Lean Manufacturing améliore considérablement la satisfaction client à travers une meilleure qualité des produits, des délais de livraison plus courts et plus fiables. Aussi, une plus grande flexibilité pour répondre aux demandes spécifiques ainsi qu’une capacité accrue à innover et à améliorer continuellement les produits.
Le système tiré (pull) permet de synchroniser la production avec la demande réelle, réduisant ainsi les ruptures de stock tout en évitant la surproduction de références peu demandées.
Renforcement de l’engagement des employés
L’approche Lean considère les employés comme la ressource la plus précieuse de l’entreprise. Elle les implique activement dans l’amélioration des processus à travers la formation et le développement des compétences. Elle permet également l’autonomisation des équipes de travail avec notamment la participation aux activités Kaizen (amélioration continue), adoptant ainsi la résolution collaborative des problèmes.
Cette implication accrue se traduit par une motivation plus forte, moins d’absentéisme et une meilleure rétention des talents. De plus, les employés développent un sentiment d’appartenance en contribuant directement à l’amélioration de l’entreprise.
Comment mettre en place le lean manufacturing dans votre organisation ?
Il existe un nombre important de méthologies lean
Identifier et éliminer les gaspillages
La première étape consiste à analyser les opérations actuelles pour identifier les différentes formes de gaspillage :
- Former les équipes à reconnaître les 8 types de gaspillages
- Organiser des “chasses aux mudas” sur le terrain
- Mettre en place la méthodologie 5S pour organiser l’espace de travail :
- Seiri (Débarrasser)
- Seiton (Ranger)
- Seiso (Nettoyer)
- Seiketsu (Standardiser)
- Shitsuke (Maintenir)
- Documenter et quantifier les gaspillages identifiés
- Prioriser les actions selon leur impact potentiel
La méthode 5S constitue souvent le point d’entrée idéal dans une démarche Lean, car elle produit des résultats visibles rapidement et prépare le terrain pour des améliorations plus complexes.
Cartographier la chaîne de valeur
La cartographie de la chaîne de valeur (Value Stream Mapping) est un outil puissant qui permet de visualiser l’ensemble du processus de production, depuis les fournisseurs jusqu’aux clients :
- Sélectionner une famille de produits à analyser
- Dessiner l’état actuel en incluant :
- Flux physiques des matériaux
- Flux d’informations
- Temps de cycle, temps de changement, niveaux de stocks
- Indicateurs de performance comme le takt time (rythme de la demande client)
- Analyser les opportunités d’amélioration
- Dessiner l’état futur souhaité
- Développer un plan d’action pour passer de l’état actuel à l’état futur
Cette cartographie permet d’identifier les étapes sans valeur ajoutée et de visualiser comment le flux peut être optimisé pour réduire les délais et améliorer la réactivité.
Créer un flux de production continu
Pour créer un flux continu, plusieurs techniques peuvent être mises en œuvre :
- Réaménager les ateliers en cellules de production organisées par famille de produits
- Équilibrer les postes de travail pour éviter les goulots d’étranglement
- Réduire les temps de changement avec la méthode SMED (Single-Minute Exchange of Die)
- Standardiser les processus pour assurer leur répétabilité et leur fiabilité
- Mettre en place une gestion visuelle pour faciliter la supervision du flux
La réduction des temps de changement est particulièrement critique pour permettre une production en petites séries sans perte d’efficacité. La méthode SMED permet souvent de réduire ce temps de plus de 50%.
Mettre en place un système tiré (pull)
En cliquant sur le Kanban, vous récupérez le modèle créé pour vous
Le système tiré est l’un des concepts fondamentaux du Lean Manufacturing :
- Définir les règles de déclenchement de la production basées sur la consommation réelle
- Mettre en place un système Kanban (cartes, conteneurs ou signaux électroniques)
- Calculer le nombre optimal de Kanbans pour chaque référence
- Former les opérateurs à respecter la discipline du système tiré
- Établir des supermarchés de pièces aux interfaces entre processus
Le système Kanban agit comme un régulateur qui limite le stock en cours et synchronise la production avec la consommation réelle, évitant ainsi la surproduction tout en garantissant la disponibilité des produits.
Poursuivre la perfection avec l’amélioration continue
L’amélioration continue (Kaizen) est la clé de la pérennité de la démarche Lean :
- Établir des indicateurs de performance clairs et visibles (tableaux de bord)
- Organiser des réunions quotidiennes courtes pour suivre les performances et résoudre les problèmes
- Mettre en place des rituels d’amélioration continue (ateliers Kaizen, PDCA - Plan-Do-Check-Act)
- Former les équipes aux outils de résolution de problèmes (5 Pourquoi, Diagramme d’Ishikawa, etc.)
- Intégrer progressivement des méthodes plus avancées comme le Lean Six Sigma
Pour les entreprises plus matures dans leur démarche Lean, l’intégration avec la méthodologie Lean Six Sigma permet d’ajouter une dimension statistique à l’amélioration des processus, notamment pour réduire la variabilité et améliorer encore davantage la qualité.
Conclusion
Le Management Lean Manufacturing représente bien plus qu’une simple méthode d’optimisation de la production ; c’est une véritable philosophie d’entreprise qui place la création de valeur et l’élimination des gaspillages au cœur de toutes les décisions. En adoptant progressivement ses principes et ses outils, les entreprises peuvent non seulement améliorer significativement leur performance opérationnelle, mais aussi créer un environnement de travail plus engageant et une culture d’amélioration continue.
La mise en œuvre du Lean n’est pas un projet ponctuel mais un parcours continu qui demande un engagement à long terme de la direction et de l’ensemble des employés. Les organisations qui réussissent le mieux sont celles qui adaptent les principes du Lean à leur contexte spécifique plutôt que d’appliquer aveuglément des outils.
En ces temps de transformation numérique, le Lean Manufacturing continue d’évoluer pour intégrer les nouvelles technologies de l’Industrie 4.0, créant ainsi un “Lean Digital” qui combine l’élimination des gaspillages physiques avec l’optimisation des flux d’information digitaux.
La question n’est plus de savoir si votre entreprise devrait adopter le Lean Manufacturing, mais plutôt comment l’implémenter de manière efficace pour rester compétitif dans un marché mondial en constante évolution.
Pour aller plus loin
3 possibilités s'offrent à vous si ce sujet vous intéresse :
-
1
Testez gratuitement Kantree ici, vous ne perdez rien, c’est gratuit !
-
2
Si vous souhaitez en apprendre plus sur comment Kantree peut s’adapter à vos défis, explorez les différents cas d’usage ici.
-
3
Vous voulez rejoindre les +1500 professionnels recevant nos conseils et actus sur la digitalisation, la collaboration, la productivité ? Inscrivez-vous à notre newsletter juste ici.
Si cet article vous a été utile, pensez à le partager. Vous pouvez le faire facilement ci-dessous.