How to optimize your processes with continuous improvement tools?
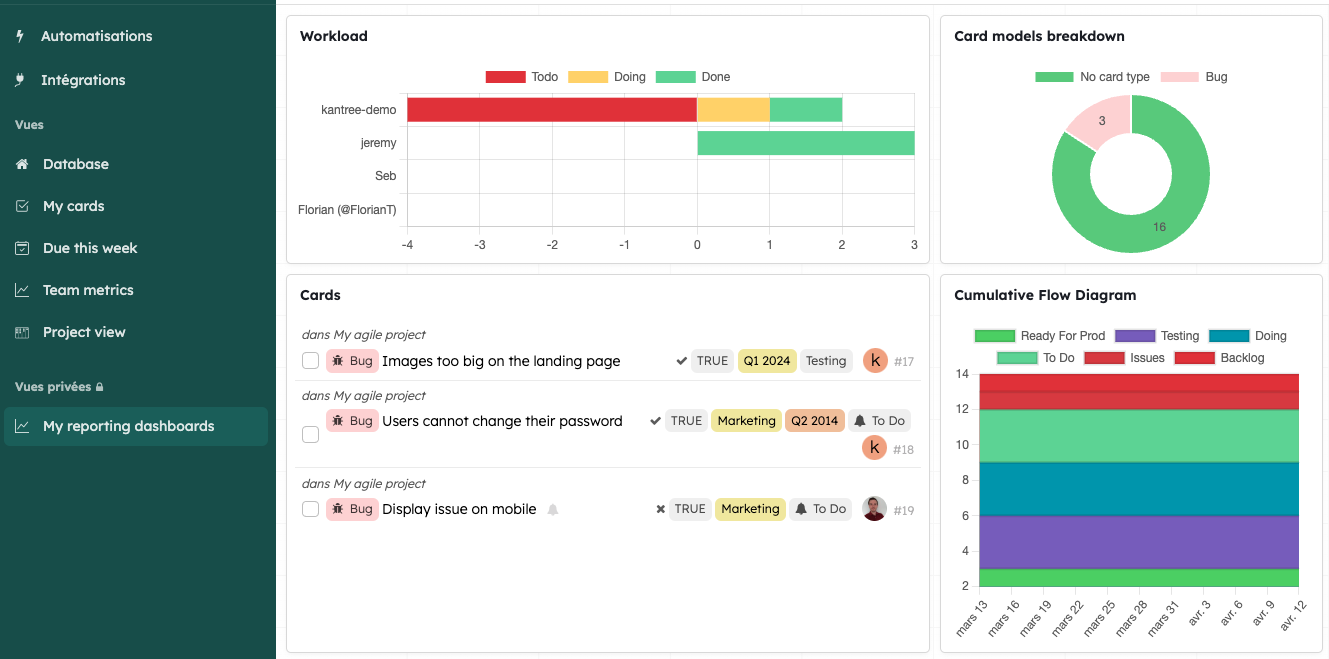
How to optimize your processes with continuous improvement tools?
The glossary of continuous improvement tools and their practical applications
In an industrial world where competitiveness is based on operational excellence, continuous improvement has become an essential strategy. It is no longer limited to isolated initiatives but constitutes a methodical framework for analyzing, optimizing and controlling production processes, logistics flows and value chains.
At the heart of this approach are proven tools, designed to identify bottlenecks, reduce waste and ensure informed decision-making.
Tools such as the QQOQCP, the 5 Whys, the DMAIC cycle or even root cause analysis (RCA: Root Cause Analysis) are not simple techniques. They represent a real toolbox for manufacturers wishing to structure their problem-solving approaches. These methods allow for a systemic approach and to mobilize teams around projects to transform daily challenges into opportunities for improvement.
This article offers an in-depth exploration of the main continuous improvement tools by placing them in the specific context of the industry.
For quick access to the desired categories, click on the links directly:
QQOQCP: how to structure your thinking with a universal method
Definition
The QQOQCP (Who, What, Where, When, How, Why) is a structured analysis method for clarifying a situation or solving a problem by answering six fundamental questions. It derives from the “circumstances” defined by the Greek rhetorician Hermagoras of Temnos in the 2nd century B.C. These questions were originally formulated in Latin: “Quis, Quid, Ubi, Quibus auxiliis, Cur, Quomodo, Quando”. The method was rediscovered and adapted in the 20th century in the field of journalism, before being widely adopted in management and project management.
When to use it?
It is particularly useful in contexts where a clear, shared analysis is required.
- When launching a project, to define responsibilities and objectives.
- In initial diagnostic phases to identify the issues at stake.
- In collaborative meetings, to structure a discussion.
How to implement it?
- Formulate each question: adapt the six questions to the specific context.
- Collect the answers: involve all stakeholders to enrich the analysis.
- Analyze and act: transform the answers into a concrete action plan.
A concrete example to better understand it
Let’s take the example of a logistics company looking to reduce its delivery times. Here’s the example applied to each stage:
Who ? The transport department.
What ? Reduce lead times by 20%.
Where ? Regional warehouses.
When ? Within three months.
How ? To optimize routes.
Why ? improve customer satisfaction.
How do you digitize your QQOQCP on Kantree?
There are a number of features you can call up to implement a QQOQCP on Kantree. Here’s an overview:
- Use customizable fields to create a card structure dedicated to QQOQCP, with specific fields for each question.
- Create a QQOQCP form to systematically collect this information when launching a project or analysis.
- Use kanban views to visualize the progress of each QQOQCP analysis.
The cards are fully modular
PDCA: a cycle for sustainable improvements
Definition
PDCA (Plan, Do, Check, Act) is an iterative method for testing and standardizing process improvements. The PDCA cycle was developed by Walter A. Shewhart in the 1930s, but was popularized and perfected by William Edwards Deming. Deming introduced this method to Japan after the Second World War, where it had a significant influence on management practices, notably at Toyota.
When to use it
This method can be applied in situations requiring a structured approach:
- For one-off or continuous improvement.
- To standardize a good practice after it has been tested.
- In projects where an incremental approach is preferable.
How to implement it?
- Plan: Clearly define the objective and prepare the action.
- Do: Test the solution on a small scale.
- Check: Analyze results and measure deviations.
- Act: Standardize or adjust according to findings.
A concrete example for a better understanding
Let’s take the case of a factory wishing to reduce its energy consumption. Here’s how it works:
- Plan: Identify the most energy-intensive equipment.
- Do: Test optimized machine schedules.
- Check: Compare consumption before and after.
- Act: Apply the schedule to all production if the results are positive.
How do you digitize your PDCA on Kantree?
There are several ways of doing it. Here are the basic steps:
- Customizable workflows to represent each step of the PDCA.
- Multiple choice” fields to indicate the status of each action (Planned, In progress, Checked, Completed).
- Timeline views to plan and track deadlines for each phase.
- Automations to move automatically from one stage of the cycle to another.
RCA (Root Cause Analysis): identifying and treating the root cause
Definition
RCA (Root Cause Analysis) is a methodology used to identify and eliminate the root causes of a problem, in order to prevent its recurrence. NASA played a crucial role in the development and popularization of this method following the Apollo 13 accident in 1970.
When to use it?
Its use is crucial when :
- major or recurring incidents need to be analyzed.
- a superficial approach has failed to resolve the problem.
How to use it?
- Gather the facts: collect all available data.
- Use visual tools: the Ishikawa diagram (or cause-and-effect diagram) is particularly effective.
- Propose solutions: each identified cause must have a dedicated corrective action.
A concrete example for a better understanding
Let’s say there’s a problem of frequent breakdowns in a particular machine. The RCA analysis reveals inadequate maintenance, so the corrective action may be to train technicians or to add quality control to interventions.
How to digitize your RCA on Kantree?
- Use the infinite hierarchy of maps to break down problems into sub-problems.
- Create a custom root cause field to identify and categorize root causes.
- Use card relationships to link problems to their causes and corrective actions.
DMAIC: A systematic approach for complex projects
Definition
DMAIC (Define, Measure, Analyze, Improve, Control) is a continuous improvement methodology used primarily in Six Sigma projects. It was developed by Motorola in the 1980s as part of their Six Sigma program. It was then adopted and perfected by General Electric under the leadership of Jack Welch in the 1990s, contributing to its worldwide popularization.
When to use it?
It is ideal for complex projects requiring measurable, sustainable improvement.
How to implement it?
- Define: Identify the problem and the objectives.
- Measure: Collect accurate data.
- Analyze: Diagnose the causes of deviations.
- Improve: Test and deploy solutions.
- Control: Constantly monitor results.
A concrete example for a better understanding
Let’s take a company wishing to reduce defects in a production line. Its DMAIC study would be 1. in-depth data analysis, 2. identification of the root cause (inadequate tooling) and then 3. implementation of new equipment.
How to digitize your DMAIC on Kantree?
- Create a specific workflow for each DMAIC step.
- Use dashboards to track KPIs at each stage of the process.
- Integrate “number” or “percentage” fields to measure and analyze data.
- Use the Gantt view to plan and monitor the various phases of your DMAIC project.
DMS (Daily Management System): Structured daily management
Definition
The DMS is a daily performance management system, designed to monitor activities in real time, detect deviations and engage teams in rapid corrective action. It was developed by Toyota in the 1950s and 1960s as an integral part of their lean manufacturing approach.
When to use it?
It fits into operational environments where constant monitoring is essential. For example, in
- in environments requiring daily monitoring.
- to quickly detect and deal with deviations.
- when implementing a culture of continuous improvement.
How to implement it?
- Define key indicators: choose relevant metrics (quality, deadlines, safety).
- Set up rituals: organize short, regular meetings with dashboard support.
- Use a collaborative tool: centralize data to facilitate analysis and decision-making.
A concrete example for a better understanding
In a factory, we can imagine a screen displaying a DMS table showing production levels, deviations and current actions in real time.
How can you digitize your DMS on Kantree?
- Create daily dashboards with essential KPIs.
- Use the calendar view to plan and track daily meetings.
- Set up automations to send you daily reports.
- Use the portfolio function to get an overview of multiple workspaces.
Dashboards are fully customizable
Kaizen: continuous improvement on a small scale
Definition
Kaizen originates from Japanese culture, and means “change for the better”. It is based on the progressive and continuous improvement of processes, involving all stakeholders. It was introduced in Japan after the Second World War by American experts such as W. Edwards Deming and Joseph Juran. Masaaki Imai popularized the term and the Kaizen philosophy in his book “Kaizen: The Key to Japan’s Competitive Success”, published in 1986.
When to use it?
Kaizen is particularly suited to contexts where gradual change is necessary.
How to implement it?
- Identify opportunities: observe day-to-day processes (as we’ll see later with the Gemba).
- Involve teams: encourage suggestions for improvement.
- Test and standardize: apply viable solutions across the board.
A concrete example for a better understanding
It could be at employee level. He suggests reorganizing his workstation to reduce unnecessary movements and increase productivity.
How to digitalize your Kaizen process on Kantree?
- Create a dedicated form for submitting improvement ideas.
- Use a specific workflow to track the validation and implementation of Kaizen ideas.
- Set up dashboards to track the gains made through Kaizen initiatives.
Set up a complete workflow with card limits per column (WIP)
5S: organization and cleanliness for efficiency {#5S}
Definition
5S (Seiri, Seiton, Seiso, Seiketsu, Shitsuke){:target=“_blank” rel=“noopener”} is a Japanese methodology for organizing, cleaning and maintaining an optimal work environment. The methodology was developed in Japan as part of the Toyota Production System in the 1960s. Hiroyuki Hirano played an important role in formalizing and disseminating the method in the 1990s.
When to use it?
This method is particularly effective in the following cases:
- to improve safety and efficiency in workshops or offices.
- when implementing a cleanliness and organization approach.
- when processes require a clear visual basis.
How to use it
- Sort (Seiri): eliminate what you don’t need.
- Arrange (Seiton): put everything in its place.
- Cleaning (Seiso): Maintain daily cleanliness.
- Standardization (Seiketsu): document best practices.
- Discipline (Shitsuke): reinforce habits through training.
A concrete example for a better understanding
In a workshop, implementing 5S reduces accidents by eliminating unnecessary objects and standardizing the location of tools.
How do you digitize your 5S on Kantree?
- Create a checklist (checklist) for each S using “yes/no checkbox” fields.
- Use different colored labels to visually identify the status of each zone or process.
- Set up regular 5S audit forms.
- Use the quadrant view to visualize 5S progress in different areas.
5 Why: getting to the root of problems
Definition
The 5 Whys method is a simple technique for identifying the root cause of a problem by asking the question “Why?” five times. The technique was developed by Sakichi Toyoda the founder of Toyota Industries, in the 1930s. It was then integrated into the Toyota Production System by Taiichi Ohno in the 1950s.
When to use it
This method is ideal for simple problems requiring a rapid response.
How to use it?
- Describe the problem: Be as factual as possible.
- Ask “Why?” five times: Go deeper with each answer.
- Propose a solution: Act on the root cause identified.
A concrete example for a better understanding
Let’s take the example of an identified quality defect. Let’s look at the questions we need to ask ourselves:
Why? the machine produced a faulty part
Why? Maintenance was inadequate.
Why? Maintenance schedule not adhered to.
Why? Lack of resources in the maintenance team.
Why? Lack of recruitment despite growing needs.
How to digitize your 5P on Kantree?
- Create a card structure with 5 numbered text fields for each “Why”.
- Use the map hierarchy to link the initial problem to the root causes identified.
- Set up a workflow to follow the analysis and resolution process.
AIC (Short team meeting): visual and reactive management
Definition
AICs consist of short, frequent meetings to monitor performance, share critical information and solve problems quickly. Although its precise origins are less well documented, it follows in the footsteps of the visual management practices developed by Toyota as part of TPS from the 1950s onwards.
When to use it?
- For teams in the field (workshop, production, logistics).
- In dynamic environments requiring rapid adjustments.
How to implement it?
- Hold on-the-spot meetings: use visual aids such as performance charts.
- Set a short duration: between 10 and 15 minutes.
- Structure discussions: discuss performance, deviations and actions.
A concrete example for a better understanding
On a production line, AICs can be used to detect and immediately correct any deviation in output.
How do you digitize your AICs on Kantree?
- Use the calendar view to plan regular AICs.
- Create specific dashboards for each AIC, displaying the relevant KPIs.
- Set up automations to send you reports before each AIC.
- Use time fields to track the duration of AICs and ensure they remain short and efficient.
Gemba: go into the field to observe
Definition
Gemba means “the real place” in Japanese. This method involves going out into the field to observe operations, understand problems and interact with the employees directly concerned. The concept was popularized by Taiichi Ohno, one of the architects of the Toyota Production System, in the 1950s.
When to use it?
It is essential in situations where direct observation is needed to understand the issues at stake.
How to use it?
- Plan your visits: identify key areas.
- Observe without intervening: take notes on flows and interactions.
- Discuss with teams: ask open-ended questions to gather ideas.
A concrete example for a better understanding
During a “gemba walk”, as it’s called, a manager identifies unnecessary movements by observing operators in a warehouse. This observation leads to a reorganization of workstations.
How to digitalize your Gemba on Kantree?
- Create mobile forms to collect observations in the field.
- Use file fields to attach photos or videos taken during Gemba visits.
- Set up a workflow to track actions resulting from Gemba observations.
- Use customizable fields to geographically locate Gemba observations and actions.
Conclusion
Tools for continuous improvement and operational excellence provide a solid foundation for transforming organizations. By integrating them with digital solutions, you can maximize their impact through simplified collaboration, automated data collection and precise tracking of results. Adopt them now to reach new heights.
Frequently asked questions
How to apply the 14 Kaizen states of mind?
The 14 Kaizen states of mind, derived from Japanese philosophy, promote a culture of continuous improvement through principles such as eliminating waste, finding simple, low-cost solutions, and encouraging team collaboration. These mindsets are applied on a daily basis to every task, from problem-solving to process optimization, with an emphasis on small, regular improvements and collective commitment.
What is the aim of lean?
Lean aims to optimize processes by eliminating waste (time, resources, errors) to bring more value to the customer. The aim is to maximize efficiency while minimizing costs, by actively involving teams in a collaborative approach. For example, tools such as Kanban or 5S help to streamline workflows and improve the overall quality of products or services.
What is a continuous improvement philosophy?
The philosophy of continuous improvement is based on the idea that every organization can constantly improve, even when it has achieved its objectives. This means regularly questioning existing methods, identifying weak points and taking corrective action to move forward. This approach extends to all levels of the company, and relies on tools such as PDCA or Kaizen to anchor changes over time.
How to implement the Kaizen method? Implementing the Kaizen method requires following these key steps:
- Observe the field (Gemba): Identify opportunities for improvement directly in the workplace.
- Involve teams: Encourage employees to come up with concrete ideas for improvement.
- Test solutions: Apply small-scale changes to verify their effectiveness.
- Standardize: Integrate validated practices into processes so that they become habits.
- Monitor results: Use performance indicators to measure the benefits obtained.
How to measure continuous improvement?
Continuous improvement is measured using Key Performance Indicators (KPIs) to assess progress. These KPIs can include metrics such as lead-time reduction, productivity increase or cost reduction. Digital tools, such as dashboards or Gantt views, make it possible to monitor these indicators in real time and adjust actions accordingly.
Who is responsible for continuous improvement?
Continuous improvement is a responsibility shared by all employees. However, specific roles, such as those of operational managers or lean management experts, are essential to steer the process, define priorities and guide teams. Management also plays a key role in setting a clear vision and allocating the necessary resources.
How to develop a continuous improvement plan?
A continuous improvement plan includes:
- An initial analysis: Evaluate current processes to identify problems.
- Clear objectives: Set measurable and realistic targets (e.g., reduce defects by 10%).
- Prioritization of actions: Rank initiatives according to their impact and feasibility.
- Structured monitoring: Deploy a tool such as PDCA or DMAIC to test, adjust, and standardize solutions.
- Transparent communication: Regularly inform teams of progress.
How to quantify continuous improvement?
To quantify continuous improvement, you need to convert the results of actions into tangible data. This can include:
- A decrease in production costs.
- An increase in turnover thanks to optimized processes.
- A measurable time saving on specific tasks. Digital tools such as ERP solutions or collaborative platforms make it possible to collect and analyze this data efficiently.
What is the role of performance indicators in driving continuous improvement?
Performance indicators (KPIs) are essential for monitoring the progress of actions and adjusting strategies in real time. They allow you to:
- Quickly identify gaps between objectives and results.
- Motivate teams by making progress visible.
- Standardize best practices once results are achieved. A good management system, such as a DMS or a digitalized Kanban board, helps to centralize these KPIs for effective management.
Cheatsheet: the glossary of continuous improvement tools (in french)
To go further
3 possibilities are available to you if this subject interests you:
-
1
Try Kantree here, it is free and you don’t need any credit card
-
2
If you want to learn more about how Kantree can adapt to your challenges, make an appointment with an expert on your use case.
-
3
Are you willing to join +1500 professionals receiving our advices and news on digitalization, collaboration, productivity? Register to our newsletter here.
If this article was useful to you, consider sharing it. You can do it easily below.